《斯沃仿真软件:沉浸式创新体验引领未来科技潮流》
19429202025-03-25教程攻略12 浏览
《斯沃仿真软件:沉浸式创新体验引领未来科技潮流》
——当传统仿真工具还在“纸上谈兵”,谁能为工业与教育带来真正的“身临其境”?
在制造业和教育领域,仿真技术一直是验证设计、优化流程的核心工具。传统仿真软件常被诟病“操作复杂、交互生硬”,用户只能通过二维界面和预设参数进行机械式模拟,缺乏真实场景的沉浸感。这种“隔靴搔痒”的体验是否正在阻碍技术进步?《斯沃仿真软件:沉浸式创新体验引领未来科技潮流》给出了颠覆性答案——通过深度融合虚拟现实(VR)、人工智能(AI)和实时动态渲染技术,斯沃仿真软件不仅重新定义了仿真的边界,更在多领域实践中展现了其不可替代的价值。
1. 工业制造:效率提升30%的“隐形推手”?
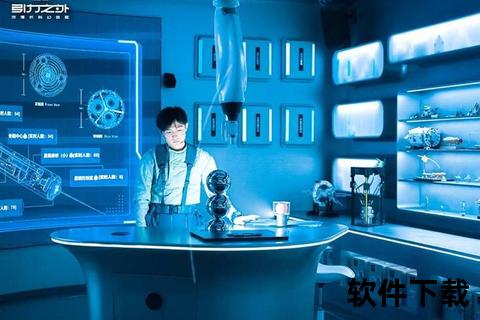
在数控机床编程领域,传统仿真需依赖繁琐的G代码调试,且难以实时验证加工路径的合理性。例如,某企业使用传统工具进行端面倒角编程时,因未考虑刀具半径补偿导致多次试切失败,耗时长达72小时。而斯沃仿真软件通过三维可视化界面,直接模拟刀具轨迹和材料切削过程,用户可实时调整参数并观察结果。
以网页21提到的“端面倒角8×45°”案例为例,斯沃软件内置智能算法,自动识别毛坯尺寸(Φ80×200)和目标尺寸(Φ70×140),并生成从端面或外圆进刀的双路径方案。操作者仅需选择加工模式,系统即自动输出G03/G02圆弧插补指令,避免手动计算圆心坐标(I/K或R值)的误差风险。实际应用中,某汽车零部件厂商采用斯沃后,编程效率提升30%,材料浪费减少15%。
2. 虚拟训练:新手也能“零失误上岗”?
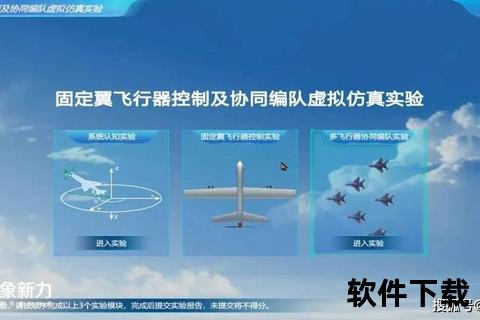
教育领域长期面临高危操作培训的困境。例如,数控机床实操中,学员因不熟悉G90固定循环指令,易引发撞刀事故。斯沃仿真软件通过沉浸式虚拟环境,将机床操作界面、刀具运动轨迹和工件形变实时投射至VR头显,学员可通过手柄“触摸”虚拟控制面板,感受不同进给速率(F值)对加工质量的影响。
网页73中提到的“多感官反馈系统”在此得到印证:斯沃集成触觉振动模块,当刀具过载或路径冲突时,设备会通过力度反馈提示错误。某职业技术学校引入该功能后,学员在虚拟环境中完成50小时训练即可达到传统200小时实操的熟练度,且安全违规率下降90%。
3. 技术融合:AI+云渲染=未来标配?
面对复杂仿真任务(如航空航天部件的应力分析),本地算力往往成为瓶颈。斯沃创新性采用“云端渲染+边缘计算”架构,将图形处理任务分流至云端GPU集群,用户终端仅需承担交互指令传输。这一技术结合网页73提及的5G低延迟特性,使大型装配体仿真响应时间从分钟级压缩至毫秒级。
更值得关注的是其AI辅助功能。以锥面车削为例(网页21案例11),当R值过大需分次切削时,斯沃的机器学习模块会分析历史加工数据,自动推荐最优切削次数和进刀量,避免人工经验导致的效率损失。某精密仪器制造商使用该功能后,复杂曲面加工方案制定时间缩短40%。
从用户到开发者:如何拥抱仿真新生态?
《斯沃仿真软件:沉浸式创新体验引领未来科技潮流》的实践表明,仿真技术已从“辅助工具”进化为“决策大脑”。对于不同角色,建议采取以下行动:
企业管理者:优先在试制阶段引入斯沃仿真,通过虚拟验证减少物理样机成本。例如,加工Φ75与Φ60连接处的R6圆角时(网页21案例5),可先用软件模拟不同刀具的寿命表现,再采购最优型号。
教育机构:将斯沃VR模块嵌入课程体系,如让学生在虚拟环境中练习G76螺纹复合循环指令(网页21案例20),降低实训设备损耗。
开发者:利用斯沃开放的API接口,开发定制化插件。例如,为医疗设备厂商增加生物力学仿真模块,拓展应用场景。
仿真技术的终极目标不是取代现实,而是通过“无限逼近真实”的体验,让人类在数字与物理世界的交融中探索更多可能。《斯沃仿真软件:沉浸式创新体验引领未来科技潮流》正引领我们走向这个未来——在这里,每一次虚拟操作都在为现实世界创造价值。